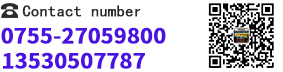
As more and more mobile phones adopt flip structures, flexible circuit boards are also being increasingly adopted. According to the combination method of substrate and copper foil, flexible circuit boards can be divided into two types: adhesive flexible boards and non adhesive flexible boards. The price of adhesive free flexible board is much higher than that of adhesive free flexible board, but its flexibility, bonding strength between copper foil and substrate, and flatness of solder pads are also better than those of adhesive free flexible board. So it is generally only used in situations with high requirements, such as COF (CHIP ON FLEX, mounting * * chips on soft boards, and requiring high flatness of solder pads).
Due to its high price, the vast majority of flexible boards currently used in the market still have adhesive flexible boards. Below, we will also introduce and discuss flexible boards with adhesive. Due to the fact that flexible plates are mainly used in situations that require bending, if the design or process is not reasonable, it is easy to produce defects such as microcracks and open welds. The following is about the structure of flexible circuit boards and their special requirements in design and manufacturing. The structure of flexible boards is divided into single-layer boards, double-layer boards, multi-layer boards, double-sided boards, etc. according to the number of layers of conductive copper foil. Single layer board structure: This type of flexible board structure is the simplest flexible board structure. Usually, the substrate+transparent adhesive+copper foil is a set of purchased raw materials, while the protective film+transparent adhesive is another type of purchased raw material. Firstly, copper foil needs to undergo etching and other processes to obtain the required circuit, and the protective film needs to be drilled to expose the corresponding solder pads. After cleaning, use the rolling method to combine the two. Then, the exposed solder pads are electroplated with gold or tin for protection. In this way, the board is ready. Usually, small circuit boards need to be stamped into corresponding shapes. There are also cases where a solder mask layer is printed directly on copper foil without the need for a protective film, which will lower the cost, but the mechanical strength of the circuit board will deteriorate. Unless the strength requirement is not high but the price needs to be as low as possible, it is best to apply protective film.